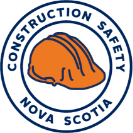
Lock-out Tag-out
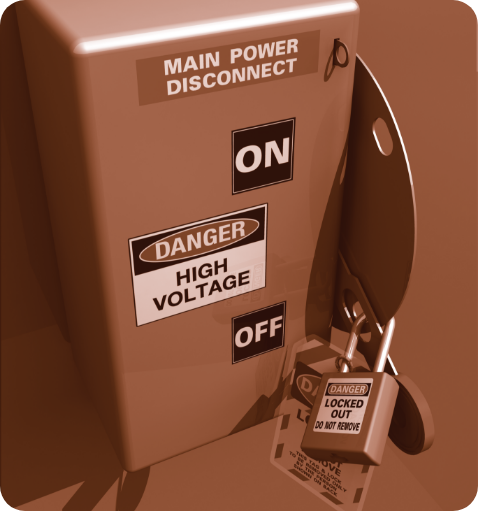
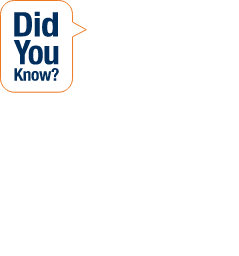
Follow these links
to related legislation
Highlighted words reveal
definitions and supplementary
information when selected
Lock-out, also known as Lock-Out Tag-Out (LOTO) or Hazardous Energy Control (HEC), is regulated in Nova Scotia under the Occupational Health & Safety Act (S.N.S. 1996, c. 7) and the Occupational Safety General Regulations (N.S. Reg. 44/99). Employers, employees, and any other competent persons are responsible for meeting the applicable occupational health and safety requirements prescribed by these regulations.
Lock-out is required where work is performed that is hazardous to a person in the workplace, if a machine, equipment, tool, or electrical installation (or any part of it) is or becomes energized. Work includes such activities as installation, maintenance, repairs, or clearing faults and jams.
Lock-out ensures that that the system is in a safe zero-energy state before any work is performed.
Lock-out is performed by systematically isolating and dissipating all hazardous energy sources, securing each identified lock-out location with a lock-out device and lock-out tag, and then verifying that a zero energy state has been reached.
Risks of not meeting the lock-out and tag-out requirements include:
- Injury or death
- Property damage
- Financial impacts such as from downtime, fines, and loss of business
- Convictions under the OHS Act
- Convictions under the Criminal Code
An employer must make sure:
- To provide and maintain equipment, machines, materials, or things that are properly equipped with safety devices.
- All employees performing lock-out are competent to do so and aware of the hazards; by providing the required information, instruction, and training.
- In addition to the normal start and stop controls, that all other means of isolating sources of energy to the equipment, tool or electrical installation are accessible to employees when needed, and easy to identify.
- Work is done according to the written lock-out procedure.
- No person works on a machine, equipment, tool, or electrical installation until it:
- is put in and maintained at a zero energy state;
- is locked out; and,
- has a lock-out tag at each lock-out location.
- The written lock-out procedure includes instructions for:
- how to achieve and maintain a zero energy state for each type of hazardous energy;
- how to lock-out the machine, equipment, tool, or electrical installation;
- how to apply the lock-out devices and lock-out tags to all identified lock-out locations;
- how to notify affected persons that the hazardous area is now safe to work in, after the lock-out steps have been completed;
- how to determine if all affected persons are clear of the hazardous area and have been notified to stay clear, before the hazardous area is energized; and
- how to energize the machine, equipment, tool, or electrical installation.
- A competent person has verified that lock-out was performed correctly, and has tested the system to verify that it is in a zero-energy state, before any work is performed.
- To designate a competent person to perform confined space assessments; including confirmation that all energy sources hazardous to a person entering, exiting, or occupying the confined space have been locked out prior to entry.
- After the work is completed, that energizing steps are done according to the written procedure, and only after all persons are clear of the hazardous area and know to remain clear of it.
- No-one other than the person who installed a lock-out device or lock-out tag removes it (Exceptions to this are listed below).
Exceptions
- If the person who installed the lock-out device or lock-out tag is not available and all reasonable attempts have been made to contact them, then:
- in a serious emergency, a person who has determined that it is safe to energize the equipment may remove a lock-out device or lock-out tag; or,
- a competent person, designated in the lock-out procedure, who has determined that it is safe to energize the equipment, may remove a lock-out device or lock-out tag.
- In cases where the lock-out requirements and/or the written lock-out procedure are inappropriate for the work to be performed, or inadequate for workers protection; then the employer may substitute an alternate written procedure that specifies:
- personnel responsibilities;
- training requirements;
- equipment requirements; and,
- the details for carrying out the work in a manner that will ensure the safety of all affected persons.
An employee must:
- Comply with the Occupational Health and Safety Act and the regulations.
- Not perform work on a machine, equipment, tool or electrical installation unless lock-out has been performed according to the written lock-out procedure; where it:
- is put in and maintained at a zero energy state;
- is locked out; and,
- has a lock-out tag at each lock-out location.
- Make sure to be fully responsible for attaching and removing their own lock-out devices and lock-out tags.
- Not remove or make ineffective a safeguard unless the machine is locked out.
- Make sure that a conveyor is locked out before standing on its supporting frame.
(i) qualified because of their knowledge, training and experience to do the assigned work in a manner that ensures the health and safety of every person in the workplace, and
(ii) knowledgeable about the provisions of the Act and regulations that apply to the assigned work, and about potential or actual danger to health or safety associated with the assigned work;
(i) isolated the energy source or sources from a machine, equipment, tool or electrical installation,
(ii) dissipated any residual energy in a system, and
(iii) secured the isolation of the energy source or sources by an inhibiting device that is operated by a key or other process,
and to have performed a “lock-out” has a similar meaning.
“Hazardous energy” is defined as "any electrical, mechanical, hydraulic, pneumatic, chemical, nuclear, thermal, gravitational, or other energy that can harm personnel" in CSA Standard Z460-13 "Control of Hazardous Energy - Lockout and Other Methods".
Certain CSA standards are available for online viewing or purchase from the CSA Group. To access these, you must first create an account with "CSA Communities". Go to: https://community.csagroup.orgOnce you are logged in, click on the "OHS Standards / View Access" option.
(a) not designed or intended for regular human occupancy;
(b) with restricted access or exit; and
(c) that is or may become hazardous to a person entering it because of its design, construction, location, atmosphere or the materials or substances in it or other conditions.
Occupational Safety General Regulations
N.S. Reg. 44/99
Part 1 Title and Definitions
Section 2 Definitions
2. In these regulations,
(a) "Act" means the Occupational Health and Safety Act ;
(aa) "adequate" means sufficient to protect a person from injury or damage to health;
(b) "ALI" means the Automotive Lift Institute;
(ba) "angle of repose" means the angle with the horizontal at which material will no longer flow freely;
(c) "ANSI" means the American National Standards Institute;
(ca) "approved" means approved by the Department or by an agency or authority designated or selected by the Department to make approvals;
(d) "ASME" means the American Society of Mechanical Engineers;
(e) "ASTM" means the American Society for Testing and Materials;
(ea) "CGA" means the Compressed Gas Association;
(f) "CGSB" means the Canadian General Standards Board;
(g) "competent person" means a person who is
(i) qualified because of their knowledge, training and experience to do the assigned work in a manner that ensures the health and safety of every person in the workplace, and
(ii) knowledgeable about the provisions of the Act and regulations that apply to the assigned work, and about potential or actual danger to health or safety associated with the assigned work;
(ga) "compressed air" means air mechanically raised to a pressure higher than atmospheric pressure;
(h) "CSA" means the Canadian Standards Association;
(i) "demolition" means the destruction or removal of all, or part, of an existing building or structure;
(ia) "Department" means the Department of Labour and Advanced Education;
(j) "designated" means, in relation to an employer, appointed in writing by the employer;
(k) "electrical installation" means the wires, machinery, apparatus, appliances, devices, material and equipment used or intended for use for the generation, transmission, distribution, supply and use of electrical power or energy, and includes a power line and power line equipment;
(l) "engineer" means a person who is registered as a member or licensed to practise under the Engineering Profession Act and is competent to do the work being performed;
(m) "firefighter" means
(i) an employee who provides fire suppression services to the public from a fire department within a municipality or local service district, or
(ii) an industrial firefighter;
(n) "guardrail" means a fall protection system consisting of vertical and horizontal members that
(i) are capable of withstanding concentrated forces, as prescribed in these regulations or an applicable standard,
(ii) warn of a fall hazard, and
(iii) reduce the risk of a fall;
(o) "hazardous substance" means chemical or biological material, dangerous goods within the meaning of the Dangerous Goods Transportation Act or a controlled product within the meaning of the Hazardous Products Act (Canada) that is likely to, because of its harmful nature, cause injury or damage to the health or safety of a person exposed to it;
(p) "hoist" means a device or equipment and its structure used for lifting or lowering material, including cranes, an automotive lift, a winch, a chain fall or other similar device, but does not include a lift truck, a power operated elevating work platform, a device to which the Elevators and Lifts Act applies or a hoist that operates in a shaft in the underground at a mine;
(pa) "ITSDF" means the Industrial Truck Standards Development Foundation;
(q) "industrial firefighter" means an employee who
(i) is designated to fight fires at the employee's place of employment, and
(ii) is employed by an employer who does not, in the normal course of its business, provide fire suppression services to the public;
(qa) "latest version" means, in relation to a standard or other publication, the latest edition of the standard or publication as supplemented, amended, added to, replaced or superseded;
(r) "lift truck" means a lift truck as defined in the latest version of ANSI standard ANSI/ITSDF B56.1, "Safety Standard for Low Lift and High Lift Trucks";
(s) "locked out" means to have
(i) isolated the energy source or sources from a machine, equipment, tool or electrical installation,
(ii) dissipated any residual energy in a system, and
(iii) secured the isolation of the energy source or sources by an inhibiting device that is operated by a key or other process,
and to have performed a "lock-out" has a similar meaning;
(t) "machine" Repealed. [N.S. Reg. 52/2000, s. 1]
(u) "manufacturer's specifications" means
(i) the written instructions of a manufacturer of a machine, material, tool or equipment that outline the manner in which the machine, material, tool or equipment is to be erected, installed, assembled, started, operated, used, handled, stored, stopped, adjusted, carried, maintained, repaired, inspected, serviced, tested, cleaned or dismantled, and
(ii) a manufacturer's instruction, operating or maintenance manual and drawings respecting a machine, tool or equipment;
(ua) "mobile crane" means a mobile crane to which the latest version of CSA standard CSA Z150 , "Safety Code on Mobile Cranes" applies;
(v) "NFPA" means the National Fire Protection Association;
(va) "overhead crane" means any mechanical device or structure that is used to raise, lower and move material that travels overhead and that incorporates a
(i) power driven drum, bridge and cable or rope,
(ii) single or multiple girder, and
(iii) moveable bridge carrying a moveable or fixed hoisting mechanism,
but does not include wall cranes, cantilever gantry cranes and semi-gantry cranes;
(vb) "personal flotation device" means personal protective equipment that is capable of supporting a person with their head above water without the direct effort of the person wearing the equipment;
(w) "power line" means the above-ground or underground wiring that is used to distribute electricity;
(x) "power line equipment" means the components that are required to distribute electricity by means of a power line;
(y) "power operated elevating work platform" means a mobile horizontal working surface that provides access and support to a person at a workplace, and that is elevated and lowered by means of a mechanism and [that complies with] Part 23: Scaffolds and Other Elevated Work Platforms, of the Workplace Health and Safety Regulations made under the Act, including a standard listed in subsection (4) thereof;
(z) "powered mobile equipment" means self-propelled equipment that is designed to operate on land in conditions other than a public highway, but does not include equipment primarily designed to transport persons, a lift truck or a power operated elevating work platform;
(aa) "SAE" means the Society of Automotive Engineers;
(ab) "structural fire-fighting" means the activities of rescue, fire suppression and conservation of property from fires involving buildings, structures, vehicles, vessels, aircraft or other large objects constructed by human effort;
(ac) "surface mine" means a work or undertaking, other than a trench, for the purpose of opening up, proving, removing or extracting any metallic or non-metallic mineral or mineral bearing substance, rock, earth, clay, sand or gravel by means of an open excavation, and includes a pit or quarry;
(ad) "tower crane" means any mechanical device or structure that
(i) incorporates a power-driven drum and cable or rope and a vertical mast or tower and a jib,
(ii) is of the traveling, fixed or climbing type, and
(iii) is used exclusively for raising, lowering and moving material;
(ae)"trench" means an excavation in which the excavation depth exceeds the excavation width;
(af) "work area" means a location at the workplace at which an employee or self-employed person is or is likely to be working;
(ag) "worked" means drilled, blasted, extracted, excavated, loaded or subjected to other similar work.
[N.S. Reg. 52/2000, s. 1; 151/2003; 53/2013, ss. 1, 93]
Part 6 Lock-out
Section 51 Interpretation, application, control and energizing
51. (1) In this Part,
(a) "equipment" includes
(i) pipes for transporting a material, and
(ii) hydraulic or pneumatic lines;
(b) "lock-out device" means the device that secures the isolation of the energy source of a locked out machine, equipment, tool or electrical installation;
(c) "lock-out location" means the location of a lock-out device;
(d) "lock-out tag" means a tag that
(i) is installed at a lock-out location,
(ii) has words directing a person not to start or operate the machine, equipment, tool or electrical installation,
(iii) identifies the person who has performed a lock-out, and (iv) does not readily conduct electricity; and
(e) "zero energy state" means a condition in which a machine, equipment, tool or electrical installation is rendered incapable of spontaneous or unexpected action or otherwise releasing kinetic or potential energy.
(2) This Part applies to a machine, equipment, tool or electrical installation that is erected, installed, assembled, started, operated, handled, stored, stopped, inspected, serviced, tested, cleaned, adjusted, maintained, repaired or dismantled.
(3) An employer shall ensure that, in addition to any normal start and stop control mechanism, a machine, equipment, tool or electrical installation has a means of isolating all sources of energy to the machine, equipment, tool or electrical installation that is
(a) accessible when needed by an employee; and
(b) readily identifiable.
(4) An employer shall ensure that where a person may be exposed to a hazard by the manual or automatic energizing of a machine, equipment, tool or electrical installation, or any part of it, a de-energized machine, equipment, tool or electrical installation, or any part of it, is energized
(a) only in accordance with an applicable written procedure established by the employer; and
(b) only after all persons are clear of the hazardous area and have been instructed to remain clear.
[N.S. Reg. 52/2000, s. 23; 53/2013, s. 27]
Section 52 Lock-out procedure
52. (1) Where work is performed on a machine, equipment, tool or electrical installation, and the work is hazardous to a person in the workplace if the machine, equipment, tool or electrical installation is or becomes energized, an employer shall ensure that
(a) the work is done in accordance with a written lock-out procedure established by the employer;
(b) no person works on the machine, equipment, tool or electrical installation until the machine, equipment, tool or electrical installation
(i) is put in and maintained at a zero energy state,
(ii) is locked out, and
(iii) has a lock-out tag at each lock-out location; and
(c) a competent person verifies that the requirements of clauses (a) and (b) have been complied with and tests to determine that the machine, equipment, tool or electrical installation is in a zero energy state.
(1A) No employee shall perform work on a machine, equipment, tool or electrical installation in the circumstances described in subsection (1) unless the requirements of clause 52(1)(b) are met.
(2) The written lock-out procedure referred to in subsection (1) shall include
(a) provision for complying with the requirements of subsection (1);
(b) the method of notifying a person in the work area of safe conditions for work after a lock-out has been completed;
(c) the method of determining that all persons near the locked out machine, equipment, tool or electrical installation are clear of the hazardous area and have been instructed to remain clear before the machine, equipment, tool or electrical installation, or any part of it, is energized; and
(d) the method of energizing the machine, equipment, tool or electrical installation.
[N.S. Reg. 52/2000, ss. 24, 25]
Section 53
53. (1) No person other than the person who installed it shall remove a lock-out device or a lock-out tag on a machine, equipment, tool or electrical installation.
(2) Despite subsection (1), where reasonable attempts have been made to contact the person who locked out the machine, equipment, tool or electrical installation and that person is not available,
(a) in a serious emergency, a person who has determined that it is safe to energize the equipment may remove a lock-out device or a lock-out tag; or
(b) a competent person who
(i) is designated in the written lock-out procedure, and
(ii) has determined that it is safe to energize the equipment,
may remove a lock-out device or a lock-out tag.
Section 54
54. Despite subsection 51(4) or Section 52, where work is performed on a machine, equipment, tool or electrical installation, and the work is hazardous to a person in the workplace if the machine, equipment, tool or electrical installation is or becomes energized, and the requirements of subsection 51(4) or Section 52 are
(a) inappropriate for the work to be performed or inadequate for the protection of persons at the workplace; or
(b) not reasonably practicable where the electrical installation is used for the generation or transmission of electricity,
an employer may substitute for the requirements of those provisions an alternative adequate written procedure that specifies personnel responsibilities, training and equipment requirements and the details for carrying out the work in a manner that will ensure the safety of all person who may be exposed to a hazard arising from the work.
Part 8 Mechanical Safety
Section 87 Safeguards
87. (1) In this Section "safeguard" means a guard, shield, guardrail, fence, gate, barrier, safety net, wire mesh or other protective enclosure or device, but does not include personal protective equipment.
(2) Where a person may come in contact with a moving part of a machine or tool that may present a hazard to a person, an employer shall ensure that an adequate safeguard has been installed on the machine or tool to prevent contact.
(3) Despite subsection (2), an employer is not required to ensure that a safeguard is installed on a machine that is equipped with a device that stops the machine automatically before a person comes into contact with the moving parts.
(4) Despite subsection (2), where it is not reasonably practicable to use a safeguard on a cutting or shaping machine and there is a possibility of injury to a person, an employer shall
(a) ensure that a push block, push stick or other adequate protective device is used; and
(b) establish a written procedure to ensure the safety of an operator of the machine.
(5) No person shall remove or render ineffective a safeguard on a machine, unless
(a) the removal or rendering is necessary to enable the cleaning, maintenance, adjustment, testing or repair of the machine;
(b) the machine is locked out; and
(c) the person replaces the safeguard and ensures the safeguard is functioning properly before leaving the machine.
(6) An employer shall ensure that adequate safeguards are installed on a machine where a person may be injured by a flying object from a machine.
(7) Where an object or material is to be applied to, fed into or supplied to a machine or tool and the object or material may shatter, splinter, vibrate, create a flying projectile or otherwise cause hazardous movement because it is not secure, an employer shall ensure that the object or material is held by a restraining device or other means of providing an equivalent level of safety.
(8) Where opening an access door exposes the moving parts of a machine or tool, an employer shall ensure, where reasonably practicable, that the access door is fitted with interlocks that
(a) prevent the access door from opening while the moving parts are in motion; or
(b) disconnect the power from the driving mechanism, causing the moving parts to stop immediately if the door is opened.
(9) Where it is not reasonably practicable to fit an access door with interlocks in accordance with subsection (8), an employer shall, in consultation with the committee or representative, if any, establish an adequate written work procedure.
[N.S. Reg. 52/2000, s. 46; 53/2013, s. 38]
Section 94
94. (1) Where a person is required to cross over a conveyor, an employer shall
(a) provide an adequate means of crossing the conveyor; and
(b) identify the crossing point by adequate means.
(2) No person in a workplace shall
(a) ride on a conveyor; or
(b) stand on the supporting frame of a conveyor.
(3) Despite clause (2)(b), a person may stand on the supporting frame of a conveyor if the conveyor has been locked out.
Part 12 Confined Space Entry
Section 129 Application and interpretation
129. (1) In this Part, "confined space" means an enclosed or partially enclosed space
(a) not designed or intended for regular human occupancy;
(b) with restricted access or exit; and
(c) that is or may become hazardous to a person entering it because of its design, construction, location, atmosphere or the materials or substances in it or other conditions.
(1A) When assessing whether a space is or may become hazardous to a person entering it because of its atmosphere under clause (1)(c), a person must not take into account the protection afforded to a person through the use of personal protective equipment or ventilation.
(2) Sections 130 to 137 do not apply to
(a) a development heading in an underground mine; and
(b) a firefighter engaged in structural fire-fighting or rescue, if the firefighter has received adequate training for confined space entry and rescue.
[N.S. Reg. 52/2000, s. 66; 53/2013, s. 53]
Section 130 Assessment and written procedures
130. (1) An employer shall ensure that no person enters a confined space until the employer has fulfilled the requirements of this Section and a competent person has provided a written certificate, in accordance with Section 131.
(2) Where a workplace includes a confined space, the employer shall ensure that a person who may be required to enter the confined space has the information necessary to identify it as such.
(3) Where at least one confined space has been identified, an employer shall establish a written confined space entry procedure that includes provision
(a) that prior to the entry of a person into the confined space, an assessment of the confined space is
(i) done in accordance with subsection (8), and
(ii) recorded by the person conducting the assessment in accordance with Section 131;
(b) for the training required by a person who may enter a confined space in the course of the person's work, and for the training required by a person who may undertake rescue operations with regard to a confined space, including training on
(i) proper use of personal protective equipment,
(ii) written rescue procedures,
(iii) maintaining contact between a person in the confined space and an attendant required under clause 134(2)(a) and the means by which the written rescue procedure is initiated in the event of an emergency in the confined space,
(iv) the limitations on the type of work that can be performed in the confined space, and
(v) the means of identifying a hazard while in a confined space;
(c) for the process for notifying a person entering a confined space of the specific type of work that may be performed in the confined space;
(d) for the method to be followed by a person entering into, exiting from or occupying the confined space;
(e) for the protective equipment that is to be used by every person entering the confined space;
(f) for the written emergency procedures to be followed in the event of an accident or other emergency in or near the confined space, including
(i) immediate evacuation of the confined space when an alarm is activated or there is any significant, unexpected and potentially hazardous change in the concentration, level or percentage referred to in subsection (8),
(ii) a determination of whether more than one person is required to be present outside a confined space during the occupancy of any person, and
(iii) a written rescue procedure;
(g) for the protective equipment and emergency equipment to be used by a person who undertakes rescue operations in the event of an accident or other emergency;
(h) for a written procedure for testing the confined space in an adequate manner, at regular intervals and on a continuous basis, if necessary, to ensure the concentration or level of a hazardous substance or physical agent complies with the limits in subsection (8); and
(i) for a means of ventilating the confined space to ensure the removal or dilution of all airborne hazardous substances from the confined space.
(4) An employer shall provide to each person entering the confined space and a person who may undertake rescue operations the protective equipment and emergency equipment referred to in this Section.
(5) An employer shall ensure that
(a) a person who enters a confined space is trained at least once every 2 years in accordance with the procedures set out in clause (3)(b); and
(b) a person who undertakes rescue operations is trained at least once every year in accordance with the procedures set out in clause (3)(b).
(6) Every person who enters into, exits from or occupies the confined space shall follow the written procedures and use the protective equipment and emergency equipment as required.
(7) An employer shall review the confined space entry procedure at least once a year and amend it, if necessary.
(8) An employer shall designate a competent person who shall perform the assessment required in clause (3)(a), which shall include
(a) where the level of a chemical substance or a mixture of chemical substances may constitute a hazard, tests to ensure that the concentration of a chemical substance or a mixture of chemical substances in the confined space does not exceed its occupational exposure limit under Part 2: Occupational Health, of the Workplace Health and Safety Regulations made under the Act or 50% of its lower explosive limit;
(b) where the level of a physical agent may constitute a hazard, tests to ensure that the level of the physical agent in the confined space is not hazardous;
(c) tests to ensure that the level of oxygen in the atmosphere in the confined space is not less than 19.5 % and not more than 22.5 %, unless the employer can demonstrate that an unsafe oxygen level is not a possibility in the circumstance;
(d) a determination of whether the concentrations, levels or percentages referred to in clauses (a), (b) and (c) can be maintained during the period of proposed occupancy of the confined space;
(e) a confirmation that any liquid in which the person may drown or any free flowing solid in which a person may become entrapped has been removed from the confined space or that work practices have been established that specifically address the presence of the liquid or solid;
(f) a confirmation that entry of any liquid, free flowing solid or hazardous substance into the confined space that could endanger the health or safety of a person has been prevented by a secure means of disconnection, the fitting of blank flanges or the implementation of a double block and bleed written procedure established by the employer or similar positive actions;
(g) confirmation that a machine, equipment, tool or electrical installation that presents a hazard to a person entering into, exiting from or occupying the confined space has been locked out; and
(h) confirmation that the opening for entry into and exit from the confined space is sufficient to allow safe passage of a person who is using personal protective equipment or emergency equipment.
(9) Where there is no possibility that a hazard identified in clauses (8)(a), (b) and (c) may occur, the requirements of clause (3)(h) do not apply.
(10) The competent person referred to in subsection (8) shall, when performing the tests required under clauses (8)(a), (b) and (c), use appropriate and properly calibrated instruments that have been functionally tested and maintain a written record of the functional and calibration tests.
(11) An employer shall keep the assessment and the confined space entry procedure required under subsection (3) at the place of business of the employer nearest to the workplace at which the confined space is located.
(12) An employer shall make available a copy of the confined space entry procedure to all persons involved in the entry of a confined space.
[N.S. Reg. 52/2000, s. 67; 53/2013, s. 54]
OCCUPATIONAL HEALTH AND SAFETY ACT
S.N.S. 1996, c. 7
Section 13 DUTIES AND PRECAUTIONS
13. (1) Every employer shall take every precaution that is reasonable in the circumstances to
(a) ensure the health and safety of persons at or near the workplace;
(b) provide and maintain equipment, machines, materials or things that are properly equipped with safety devices;
(c) provide such information, instruction, training, supervision and facilities as are necessary to the health or safety of the employees;
(d) ensure that the employees, and particularly the supervisors and foremen, are made familiar with any health or safety hazards that may be met by them at the workplace;
(e) ensure that the employees are made familiar with the proper use of all devices, equipment and clothing required for their protection; and
(f) conduct the employer's undertaking so that employees are not exposed to health or safety hazards as a result of the undertaking.
(2) Every employer shall
(a) consult and co-operate with the joint occupational health and safety committee, where such a committee has been established at the workplace, or the health and safety representative, where one has been selected at the workplace;
(b) co-operate with any person performing a duty imposed or exercising a power conferred by this Act or the regulations;
(c) provide such additional training of committee members or the representative as may be prescribed by the regulations;
(d) comply with this Act and the regulations and ensure that employees at the workplace comply with this Act and the regulations; and
(e) where an occupational health and safety policy or occupational health and safety program is required pursuant to this Act or the regulations, establish the policy or program.
(3) The employer at a subsea coal mine shall provide such additional resources or information for the committee as may be prescribed by the regulations.
[N.S. 2007, c. 14, s. 7; 2010, c. 66, s. 5]
Section 17
17. (1) Every employee, while at work, shall
(a) take every reasonable precaution in the circumstances to protect the employee's own health and safety and that of other persons at or near the workplace;
(b) co-operate with the employer and with the employee's fellow employees to protect the employee's own health and safety and that of other persons at or near the workplace;
(c) take every reasonable precaution in the circumstances to ensure that protective devices, equipment or clothing required by the employer, this Act or the regulations are used or worn;
(d) consult and co-operate with the joint occupational health and safety committee, where such a committee has been established at the workplace, or the health and safety representative, where one has been selected at the workplace;
(e) co-operate with any person performing a duty or exercising a power conferred by this Act or the regulations; and
(f) comply with this Act and the regulations.
(2) Where an employee believes that any condition, device, equipment, machine, material or thing or any aspect of the workplace is or may be dangerous to the employee's health or safety or that of any other person at the workplace, the employee shall
(a) immediately report it to a supervisor;
(b) where the matter is not remedied to the employee's satisfaction, report it to the committee or the representative, if any; and
(c) where the matter is not remedied to the employee's satisfaction after the employee reports in accordance with clauses (a) and (b), report it to the Division.