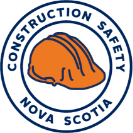
Asbestos in the Workplace
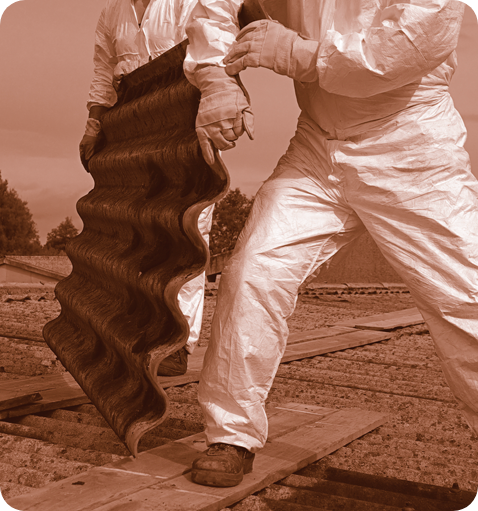
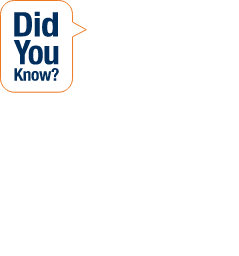
Follow these links
to related legislation
Highlighted words reveal
definitions and supplementary
information when selected
Asbestos is a friable material which means that when it is dry, it can release small fibres and clumps of fibres into the air as dust. Asbestos was used in a wide range of manufactured products, including building materials (e.g., ceiling and floor tiles, siding, plaster, insulation, shingles, etc.) because of its heat-resistant and insulating properties. These manufactured materials with asbestos are often referred to as asbestos containing materials (ACM).
When left undisturbed and in good condition, asbestos containing material does not pose a significant health risk. However, when the asbestos is disturbed, damaged, or cut, the fibres can become airborne which creates an inhalation hazard. Asbestos only poses a health risk when fibres are present in the air and people breathe them into the lungs. The health effects from long-term asbestos exposure are well documented, including asbestosis and changes in the lining of the lungs (pleural abnormalities). All forms of asbestos may cause lung cancer and mesothelioma.
Building owners and employers can use the Guide to Assessment and Management of Asbestos in the Workplace (2013) where there is reason to believe that asbestos containing materials are present. Furthermore, an occupational health and safety officer may order an owner or an employer to comply with a part of the code of practice to fulfill their duty to take all reasonable precautions for the protection of persons at or near a workplace. In addition, employers may adopt the Guide to Removal of Friable Asbestos Containing Materials as a code of practice in the workplace.
This topic reviews the requirements of owners and employers under the Asbestos in the Workplace: A Guide to Assessment and Management of Asbestos in the Workplace (2013) and A Guide to Removal of Friable Asbestos Containing Material (2013).
Assessing and Managing Asbestos Containing Materials in the Workplace
The owner of a building must:
- Have a competent person assess whether asbestos containing materials are present in the building.
- Make sure the assessment includes the collection of a representative number of bulk samples for assessment to meet the established requirements for the type of material and minimum number of bulk material samples (see table 1).
Surfacing material, including material that is applied by spraying, troweling or otherwise (e.g., acoustical plaster, fireproofing materials). |
Less than 90 square metres (<1000 ft2) | |
90 or more square metres, but less than 450 square metres (1000-5000 ft2) | ||
450 or more square metres (>5000 ft2) | ||
Thermal insulation, except thermal insulation that has been sprayed or troweled. | Any size | |
Less than 2 linear metres or 0.5 square metres | ||
Other material. | Any size |
- Make sure each bulk sample is analyzed by a suitable laboratory analytical method.
- Make sure that analysis report includes the type and the percent composition of the asbestos.
- Keep a written inventory documenting the locations where each bulk sample was collected and record the results of all bulk sample analyses.
- Maintain the inventory for as long as asbestos containing materials are present.
- Inform employers with workplaces in the building about the presence of asbestos containing material in the areas that are applicable to the employer.
- Provide employers with workplaces in the building with a reasonable opportunity to view the inventory.
Asbestos Management Plan
- Keep and maintain a written asbestos management plan if asbestos containing materials are present in a workplace. An asbestos management plan must list the areas of priority and measures that to prevent asbestos exposure in the workplace (e.g., removal, enclosure, encapsulation, or installation of a physical barrier to prevent unauthorized individuals from accessing the area with asbestos containing material).
- Consult the most recent version of the OHS Division document entitled “Asbestos in the Workplace: A Guide to Removal of Friable Asbestos Containing Material” when planning to remove friable asbestos containing material.
- Inform any employers with workplaces is in the building and contractors or constructors, for which the owner has responsibility, of the:
- locations where potential asbestos exposure exists;
- potential health risks caused by asbestos exposure;
- restrictions and precautions that must be followed to minimize the risk caused by the presence of asbestos containing material in the workplace; and
- procedures to report damage of any material believed to contain asbestos.
- Make sure any contractors, self-employed person who may come in contact with asbestos containing materials in the building are trained in safe work procedures that include:
- the proper selection, use, and care of required personal protective equipment;
- how to use isolation techniques; and
- how to use the appropriate equipment for the task.
- Regularly inspect asbestos containing material and check for signs of damage that could result in a release of asbestos fibres.
- Maintain written records of communication, training, and inspections for at least two years or for as long as they are relevant.
An employer must:
- Consult the committee or representative during the development of the asbestos management plan.
- Inform employees, contractors, and constructors, for which they have responsibility, of the:
- locations where potential asbestos exposure exists;
- potential health risks caused by asbestos exposure;
- restrictions and precautions that must be followed to minimize the risk caused by the presence of asbestos containing material in the workplace; and
- procedures to report damage of any material believed to contain asbestos.
- Train employees in safe work procedures for work that requires contact with asbestos containing material. Training must include:
- the proper selection, use, and care of required personal protective equipment;
- how to use isolation techniques; and
- how to use the appropriate equipment for the task.
- Maintain written records of communication, training, and inspections for at least two years or for as long as they are relevant.
Temporary Measures to Manage an Immediate Risk of Asbestos Exposure
The owner and any employer whose workplace is in a building with materials that contain asbestos must:
- Inform occupants, employees, contractors, dependent contractors, and constructors who face an immediate risk of excessive exposure to asbestos containing material in the workplace of the:
- locations where the potential for asbestos exposure exists;
- potential health risks posed by asbestos exposure; and
- restrictions and precautions that they must follow to minimize the risk caused by the presence of asbestos containing material in the workplace.
- Take immediate action to temporarily prevent asbestos exposure (e.g., use a physical barrier to prevent access to damaged asbestos containing material).
- Make sure a competent person removes any asbestos containing materials that may result in an immediate risk of asbestos exposure.
An officer may:
- Order an assessment under Section 52 of the Occupational Health and Safety Act.
- Order temporary measures under Section 19 (for owners) or Section 13 (for employers) of the Occupational Health and Safety Act.
- Order an asbestos management plan under Section 19 (for owners) or Section 13 (for employers) of the Occupational Health and Safety Act.
Removal of Friable Asbestos Containing Materials
An employer must:
Site Preparation
- Use a glove bag or a temporary enclosure to prevent asbestos fibres from leaving the work area when removing friable asbestos.
- Make sure an enclosure:
- is made of polyethylene sheeting that is at least 0.15 millimetres thick;
- is labeled with signs warning that only authorized employees are allowed in the enclosure;
- has an airlock, a clean room, a shower area, a decontamination room, and a holding area for waste materials;
- has at least one observation window that will, if reasonably practicable, allow people outside the enclosure to see the work activity inside;
- is kept under negative pressure using HEPA negative air units, 24-hours per day during the removal of the friable asbestos until the area has passed clearance testing after cleanup; and
- has at least 4 air changes per hour or a static pressure of negative five (-5) Pascal’s relative to pressure outside the enclosure. The pressure must be measured inside the enclosure at a point furthest from the exhaust fan.
Ventilation and HEPA Testing
- Prevent contamination of the workplace by isolating all ventilation systems servicing the enclosed work area. This does not include specific HEPA negative air units that are used to exhaust air from inside the enclosure.
- Isolate the ventilation by:
- sealing ventilation duct supply and return air openings with poly sheeting; and
- turning off the air handling systems servicing the enclosed work area, if reasonably practicable.
- Must make sure all vacuums and HEPA negative air units used to exhaust air to an area outside successfully pass a HEPA unit test:
- after replacing a HEPA filter; and
- at least once every 12 months.
- HEPA negative air units that exhaust air from inside the enclosure to an indoor area that is outside of the enclosure must pass an on site HEPA unit test immediately before being used.
- Make sure HEPA testing includes:
- a visual inspection to identify any damage and examine the integrity of the seal in the filter frame; and
- a filter testing procedure using dioctyl phthalate (DOP) or other appropriate challenge test material to verify the unit is functioning as the manufacturer intended.
- Maintain HEPA testing records with the name of the testing agency, the name of the tester, the date of testing, and the test results.
- Maintain all HEPA filters in ventilation systems and vacuum cleaners according to the manufacturer's instructions, or as specified by a professional engineer to maintain their effectiveness.
Personal Protective Equipment
- Make sure employees wear full-body protective coveralls and a half-facepiece, air-purifying, non-powered respirator with a 100-class filter, or equipment offering equal or greater protection when using a glove bag.
- Make sure employees wear full-body protective coveralls (including a hood) and a full-facepiece powered air-purifying respirator with a 100-class filter, or equipment offering equal or greater protection when using wet removal methods without a glove bag.
- Make sure during the dry removal of friable asbestos to:
- monitor according to the requirements below in "Dust Control and Monitoring";
- make sure employees wear full-body protective coveralls (including a hood) and use a full-facepiece powered air-purifying respirator with 100-class filter if asbestos exposure is less than 100 fibres per cubic centimeter (f/cc); and
- make sure employees use an atmosphere supplying respirator with an assigned protection factor of 10000 if asbestos exposure is 100 f/cc or greater.
- Comply with the latest version of CSA standard Z94.4, “Selection, Use, and Care of Respirators” when respiratory protection is required, including:
- the selection, use, maintenance, and testing of respirators;
- the training of employees who use a respirator;
- making sure employees who wear tight-fitting respirators are clean-shaven; and
- quantitative fit-testing if a protection factor of 1000 is required for a full-facepiece powered air-purifying respirator.
Dust Control and Monitoring
- Only use dry removal of friable asbestos-containing materials if wet removal will be hazardous to employees.
- Take daily personal samples of airborne asbestos fibres during dry removal where a full-facepiece powered air-purifying respirator with 100-class filter is used to verify that the airborne concentration does not exceed 100 f/cc.
- Take daily samples during dry or wet asbestos removal if a glove bag is not used and the air from inside the enclosure is exhausted to an indoor area outside of the enclosure. If the concentration exceeds 0.01 f/cc in an indoor area outside of the enclosure, the employer must take immediate action.
- Collect, prepare, analyze, and report samples according to:
- NIOSH Method 7400, Issue 2: Asbestos and Other Fibers by PCM (August 15, 1994);
- NIOSH Method 7402, Issue 2: Asbestos by TEM (August 15, 1994); or
- an equivalent method with an equivalent or greater level of precision and accuracy.
- Analyze samples within 24 hours. If an increase of airborne concentration is detected, the personal protective equipment must be reviewed and upgraded.
- Notify the committee or representative of the testing according to the requirements of Section 35 of the Occupational Health and Safety Act.
- Conduct monitoring for airborne asbestos fibres during clearance testing, as specified below under "Visual Inspection and Clearance Test".
- Maintain a record of all air sampling data according to subsection 1.15(1) of the Workplace Health and Safety Regulations.
Personal Hygiene
- Make sure, when using a glove bag, that all coveralls or other contaminated clothing are removed and prepared for disposal before removing any respirator or leaving the work area.
- Make sure that if friable ACM is removed without a glove bag, that:
- street clothes are removed and left in the clean area of the enclosure;
- protective clothing is worn in the work area;
- coveralls and other contaminated clothing are removed and prepared for disposal or cleaning before removing any respirator or leaving the work area;
- a shower with both warm and cold running water is provided; and
- respirators are worn until the hair and body are thoroughly wet.
- Provide toilet facilities in or near the clean room and on the decontaminated side of the enclosure.
- Not permit employees to eat, drink, or smoke in the work area.
- Arrange for washable coveralls to be safely stored, transported, and cleaned to make sure that no asbestos material leaves the remediation site uncontrolled.
Waste Disposal
- Dispose of asbestos waste according to the applicable provincial or federal asbestos disposal requirements.
- Make sure that all asbestos waste is placed in 0.15 millimetre polyethylene bags with printed asbestos warning labels. All bags must be closed, and the outside cleaned before taking them to the decontamination area.
- Make sure all bags containing asbestos waste are placed in a second 0.15 millimetre labeled bag or drum. The material may be packaged with another method that the Department of Environment approves in writing and sent to an approved disposal site.
- Notify the employer or representative at the disposal site of any materials that are suspected to contain asbestos.
Clean-Up
- Make sure that the inner surfaces of the enclosure and all tools and equipment are cleaned after removal of friable ACM by damp wiping or vacuuming with a vacuum that has passed a HEPA unit test after each filter change and at least once per year.
- Adequately seal any residual ACM with a suitable encapsulant that will remain inside the work area after the enclosure is removed.
Visual Inspection and Clearance Test
- Have a competent person visually inspect the work area inside the enclosure following the clean-up and prior to removing an enclosure that is not a glove bag to make sure that asbestos fibres will not become airborne.
- Keep a record of inspections as required by 1.15(2) of the Workplace Health and Safety Regulations.
- Use forced air equipment, such as a leaf blower, for at least 5 minutes per 90 square metres of floor area to dislodge fibres from the walls, ceilings, floors, ledges, and other surfaces inside the enclosure before sampling for airborne asbestos fibres inside the enclosure.
- Collect at least one sample for airborne asbestos fibres for every 270 cubic metres of containment.
- Collect, prepare, analyze, and report samples according to:
- NIOSH Method 7400, Issue 2: Asbestos and Other Fibers by PCM (August 15, 1994);
- NIOSH Method 7402, Issue 2: Asbestos by TEM (August 15, 1994); or
- an equivalent method with an equivalent or greater level of precision and accuracy.
- Make sure the airborne concentration of each aerosol sample does not exceed 0.01 f/cc of air. The clearance test cannot be passed if the analysis shows a concentration greater than 0.01 f/cc.
- Have a competent person review the results of the visual inspection and air samples before deciding whether the enclosure may be removed.
- Repeat the clean-up steps above if the competent person indicates that the visual inspection or clearance test has not passed.
- Only remove the enclosure after a competent person determines the area has passed the clearance test and visual inspection.
(i) qualified because of their knowledge, training and experience to do the assigned work in a manner that ensures the health and safety of every person in the workplace, and
(ii) knowledgeable about the provisions of the Act and regulations that apply to the assigned work, and about potential or actual danger to health or safety associated with the assigned work.
Certain CSA standards are available for online viewing or purchase from the CSA Group. To access these, you must first create an account with "CSA Communities". Go to: https://community.csagroup.org/
Once you are logged in, click on the "OHS Standards / View Access" option. Click on Nova Scotia to see the CSA Standards as referenced in N.S. legislation.
Asbestos in the Workplace: A Guide to Assessment & Management of Asbestos in the Workplace
Revised November 21, 2013
Section 1 Specific Requirements
1. Assessment of Materials
(1) The owner of a building must ensure that
(1) the building is assessed by a competent person to determine if any asbestos containing materials are present;
(2) the assessment includes the collection of a representative number of bulk samples of suspect materials (see Table 1);
(3) each bulk sample is analyzed by an appropriate laboratory analytical method; and
(4) the type of asbestos and percent composition of asbestos in each sample is indicated in the analysis report.
(An assessment could be ordered under Section 52 of the Occupational Health and Safety Act.)
Bulk Material Samples1
Type of material | Size of area of homogeneous material | Minimum number of bulk material samples to be collected |
Surfacing material, including but not limited to material that is applied by spraying, troweling or otherwise, such as acoustical plaster on ceilings, and fireproofing materials on structural members. | Less than 90 square metres (<1000 ft2) | 3 |
90 or more square metres, but less than 450 square metres (1000-5000 ft2) | 5 | |
450 or more square metres (>5000 ft2) | 7 | |
Thermal insulation, except thermal insulation that has been sprayed or troweled. | Any size | 3 |
Less than 2 linear metres or 0.5 square metres | 1 | |
Other material. | Any size | 3 |
Section 2 Inventory of Samples
2. Inventory of Samples
(1) The owner of the building shall ensure that
(a) a written inventory is created to document the locations where each bulk sample has been collected and the results of all bulk sample analyses;
(b) the inventory is maintained as long as asbestos containing materials are present in the workplace;
(c) each employer whose workplace is in the building is informed regarding the presence of asbestos containing material in relevant areas of the building; and
(d) each employer whose workplace is in the building is provided with a reasonable opportunity to view the inventory.
(2) The employer must ensure that the committee or the representative, if any, is informed regarding the presence of asbestos containing material in relevant areas of the building in accordance with Section 35 of the Occupational Health and Safety Act.
(An assessment could be ordered under Section 52 of the Occupational Health and Safety Act.)
Section 3 Temporary Measures to Manage Immediate Risk of Asbestos Exposure
3. Temporary Measures to Manage Immediate Risk of Asbestos Exposure
(1) Where asbestos containing material is present in a workplace, and there is an immediate risk of exposure, the owner and any employer whose workplace is in the building must
(a) inform occupants, employees, contractors, dependent contractors, and constructors who face an immediate risk of excessive exposure regarding the
i. locations where the potential for asbestos exposure exists in the workplace;
ii. potential health risks posed by asbestos exposure; and
iii. restrictions and precautions that must be followed to minimize the risk caused by the presence of asbestos containing material in the workplace; and
(b) take immediate action to temporarily prevent asbestos exposure (e.g. use a physical barrier to prevent access to damaged asbestos containing material); and
(c) ensure that any asbestos containing materials that may result in an immediate risk of asbestos exposure are removed by a competent person who has been trained in the applicable safe work procedures.
(Temporary measures could be ordered under Section 19 (for Owners) or Section 13 (for Employers) of the Occupational Health and Safety Act)
Section 4 Asbestos Management Plan
4. Asbestos Management Plan
Owner Responsibilities
(1) Where asbestos containing material is present in a workplace and any immediate risk has been addressed in accordance with Section 3 of this document, the owner of the building must
(a) ensure that a written asbestos management plan
i. is developed and maintained as long as an asbestos containing material is present in the workplace; and
ii. lists the areas of priority, and measures that will be taken to prevent asbestos exposure in the workplace (such as removal, enclosure, encapsulation, or use of a physical barrier to prevent unauthorized individuals from accessing the area where asbestos containing material exists);
(b) consult the most recent version of the OHS Division document entitled "Asbestos in the Workplace: A Guide to Removal of Friable Asbestos Containing Material" where the removal of friable asbestos containing material is planned;
(c) inform any employers whose workplace is in the building, and any contractors or constructors, for which the owner has responsibility, of the
i. locations where the potential for asbestos exposure exists in the workplace;
ii. potential health risks posed by asbestos exposure;
iii. restrictions or precautions that must be followed to minimize the risk associated with the presence of asbestos containing material in the workplace; and
iv. reporting procedures to be followed in the event that a material that is believed to contain asbestos is damaged;
(d) ensure that any contractor or self-employed person who the owner requires to work in the building is trained in safe work procedures for activities that may require contact with asbestos containing materials, including the proper selection, use and care of required personal protective equipment, the use of isolation techniques as needed, and the use of the appropriate equipment for the work to be done;
(e) conduct regular inspections of asbestos containing materials to check for signs of damage that could result in a release of asbestos fibres; and
(f) maintain written records of communication, training, and inspections for a period of two years or for as long as they are relevant.
Employer Responsibilities
(2) Where asbestos containing material is present in a workplace the employer of that workplace must
(a) consult the committee or representative, if any, regarding the development of the asbestos management plan;
(b) inform employees, contractors, dependent contractors, and constructors, for which they have responsibility, of the
i. locations where the potential for asbestos exposure exists in the workplace;
ii. potential health risks posed by asbestos exposure;
iii. restrictions or precautions that must be followed to minimize the risk associated with the presence of asbestos containing material in the workplace; and
iv. reporting procedures to be followed in the event that a material that is believed to contain asbestos is damaged;
(c) ensure employees are trained in safe work procedures for activities that may require contact with asbestos containing materials, including the proper selection, use and care of required personal protective equipment, the use of isolation techniques as needed, and the use of the appropriate equipment for the work to be done; and
(d) maintain written records of communication and training for a period of two years or for as long as they are relevant.
(An assessment management plan could be ordered under Section 19 (for Owners) or Section 13 (for Employers) of the Occupational Health and Safety Act)
Asbestos in the Workplace: A Guide to Removal of Friable Asbestos Containing Materials
Revised November 21, 2013
Section 1 Site Preparation
1. Site Preparation
(1) Where removal of friable asbestos is performed, a glove bag must be used, or a temporary enclosure must be constructed to prevent asbestos fibres from leaving the work area.
(2) An enclosure used during the removal of friable asbestos must
(a) be constructed of polyethylene sheeting that is at least 0.15 millimetres thick,
(b) be labeled with signs to restrict entry to authorized personnel,
(c) include provisions for an airlock, clean room, shower area, decontamination room, and holding area for waste materials;
(d) be maintained under negative pressure using HEPA negative air units, 24-hours per day for the duration of the work and until the area has passed clearance testing after cleanup;
(e) have a minimum of 4 air changes per hour or a static pressure of negative five (-5) Pascal’s relative to pressure outside the enclosure, as measured inside the enclosure at a point furthest from the exhaust fan; and
(f) have at least one observation window made of a transparent material that, where reasonably practicable, enables a person who is located outside of the enclosure to see work activity that is taking place inside the enclosure.
Section 2 Ventilation - HEPA Testing
2. Ventilation - HEPA Testing
(1) Aside from specific HEPA negative air units that are used to exhaust air from inside the enclosure, all ventilation systems that service the work area must be isolated from the enclosure to prevent contamination by
(a) sealing ventilation duct supply and return air openings with poly sheeting; and
(b) where reasonably practicable, turning off the air handling systems that service ithe work area.
(2) All vacuums and HEPA negative air units that are used to exhaust air from inside the enclosure to any area outside of the enclosure must successfully pass a HEPA unit test
(a) after a HEPA filter is replaced; and
(b) at least once every 12 months.
(3) All HEPA negative air units that are used to exhaust air from inside the enclosure to an indoor-area that is outside of the enclosure must successfully pass a HEPA unit test, onsite, immediately prior to use at a given site.
(4) HEPA testing must include
(a) a visual inspection to identify any apparent damage and to examine the integrity of the seal in the filter frame; and
(b) a filter testing procedure using dioctyl phthalate (DOP) or other appropriate challenge test material to verify the unit is functioning as the manufacturer intended.
(5) HEPA testing records must be maintained, including the name of the testing agency, the name of the tester, the date of testing, and the result of the test.
(6) The employer is also required to maintain all HEPA filters in ventilation systems and vacuum cleaners in accordance with manufacturer's instructions, or as specified by a professional engineer, to ensure that they remain effective.
Section 3 Personal Protective Equipment
3. Personal Protective Equipment
(1) Where a glove bag is used, employees must wear full-body protective coveralls and a half-facepiece, air-purifying, non-powered respirator equipped with a 100-class filter, or equipment offering equal or greater protection.
(2) Where wet removal of friable asbestos is to be performed without the use of a glove bag, employees must wear full-body protective coveralls (including hood) and a full-facepiece powered air-purifying respirator equipped with a 100-class filter, or equipment offering equal or greater protection.
(3) Where dry removal of friable asbestos is to be performed
(a) monitoring must be conducted in accordance with Section 4;
(b) employees must wear full-body protective coveralls (including hood) and are permitted to use a full-facepiece powered air-purifying respirator equipped with a 100-class filter unless the results from monitoring during removal indicate that an employee’s exposure is greater than 100 fibres per cubic centimeter; and
(c) where exposures are 100 fibres per cubic centimeter or greater, an atmospheresupplying respirator that has an assigned protection factor of 10000 is required.
(4) Where respiratory protection is required, the employer must ensure compliance with the latest version of CSA Standard Z94.4 , "Selection, Use, and Care of Respirators" for the selection, use, maintenance, and testing of a respirator, as well as the training of employees who use a respirator. This standard specifies that employees who wear a tight-fitting respirator must be clean-shaven, and that quantitative fit-testing must be carried out if a protection factor of 1000 is to be achieved with a full-facepiece powered air-purifying respirator.
Section 4 Dust Control and Monitoring
4. Dust Control and Monitoring
(1) Dry removal of friable asbestos-containing materials may be performed only where wet removal is shown to present a hazard to employees.
(2) When dry removal is conducted and where a full-facepiece powered air-purifying respirator equipped with a 100-class filter is used for worker protection, personal sampling for airborne asbestos fibres must be conducted on a daily basis during removal to verify the airborne concentrations do not exceed 100 fibres per cubic centimeter.
(3) Where dry or wet asbestos removal is conducted, a glove bag is not used, and the air from inside the enclosure is exhausted to an indoor area that is outside of the enclosure,
(a) daily sampling for airborne asbestos fibres must be conducted outside of the enclosure.
(b) immediate action must be taken if the concentration of airborne asbestos is found to exceed 0.01 fibres per cubic centimeter of air in an indoor area that is outside of the enclosure.
(4) All samples for airborne asbestos fibres must be collected, prepared, analyzed, and reported in accordance with the NIOSH Method 7400, Issue 2: Asbestos and Other Fibers by PCM (August 15, 1994), or NIOSH Method 7402, Issue 2: Asbestos by TEM (August 15, 1994), or by a method that provides for an equivalent or greater level of precision and accuracy.
(5) Samples must be analyzed within 24 hours and the committee or representative must be notified of the testing, in accordance with Section 35 of the Occupational Health and Safety Act. Where an increase in airborne concentration is detected, the personal protective equipment required must be reviewed and upgraded in accordance with this document.
(6) Monitoring for airborne asbestos fibres must be conducted during clearance testing, as specified in Section 8.
(7) The employer must maintain a record of all air sampling data in accordance with subsection 1.15(1) of the Workplace Health and Safety Regulations.
Section 5 Personal Hygiene
5. Personal Hygiene
(1) Where a glove bag is used, coveralls and other contaminated clothing must be removed and prepared for disposal prior to removing any respirator or leaving the work area.
(2) Where removal of friable asbestos-containing material is performed without a glove bag
(a) street clothes must be removed and left in the clean area of the enclosure;
(b) protective clothing, as set out in Section 3, must be worn in the work area;
(c) coveralls and other contaminated clothing must be removed and prepared for disposal or cleaning prior to removing any respirator or leaving the work area;
(d) a shower with both warm and cold running water must be provided; and
(e) respirators must be worn until the hair and body have been thoroughly wetted.
(3) Toilet facilities must be provided in or near the clean room on the decontaminated side of the enclosure.
(4) No eating, drinking, or smoking is permitted in the work area.
(5) Where washable coveralls are used, arrangements for the proper storage, transportation and cleaning must be made and followed to ensure asbestos material does not leave the remediation site uncontrolled.
Section 6 Waste Disposal
6. Waste Disposal
(1) Asbestos waste must be disposed of in accordance with all applicable provincial or federal asbestos disposal requirements.
(2) All asbestos waste must be placed in 0.15 millimetre polyethylene bags with printed asbestos warning labels.
(3) Bags containing asbestos waste must be closed, and the outside cleaned before being taken to the decontamination area.
(4) Bags containing asbestos waste must be placed within a second, 0.15 millimetre, labeled bag or a labeled drum. Alternatively, the material must be packaged and placed in accordance with a method approved in writing by the Department of Environment and sent to an approved disposal site.
(5) When asbestos waste is brought to a disposal site, the employer or representative at the disposal site must be notified of any materials that are suspected to contain asbestos.
Section 7 Clean-Up
7. Clean-Up
(1) Following the removal of friable asbestos containing materials the work area, the inner surfaces of the enclosure, as well as all tools and equipment, must be cleaned by
(a) damp wiping; or
(b) vacuuming with a vacuum that has successfully passed a HEPA unit test in accordance with the HEPA unit test after each filter change, and at least once per year.
(2) Any residual asbestos containing materials that will remain inside the work area after the enclosure is removed must be adequately sealed with a suitable encapsulant.
Section 8 Visual Inspection & Clearance Test
8. Visual Inspection & Clearance Test
(1) Following the clean-up requirements noted in Section 7, and prior to removing an enclosure that is not a glove bag, a visual inspection of the work area inside the enclosure must be carried out by a competent person to ensure that there is no reasonable possibility of asbestos fibres becoming airborne. The employer must maintain a record of these inspections in accordance with subsection 1.15(2) of the Workplace Health and Safety Regulations.
(2) Before sampling for airborne asbestos fibres inside the enclosure, forced air equipment, such as a leaf blower, must be operated for at least 5 minutes per 90 square metres of floor area to dislodge fibres from any walls, ceilings, floors, ledges, and other surfaces inside the enclosure.
(3) At least one sample for airborne asbestos fibres must be collected for every 270 cubic metres of containment.
(4) All samples for airborne asbestos fibres must be collected, prepared, analyzed, and reported in accordance with the NIOSH Method 7400, Issue 2: Asbestos and Other Fibers by PCM (August 15, 1994), or NIOSH Method 7402, Issue 2: Asbestos by TEM (August 15, 1994), or by a method that provides for an equivalent or greater level of precision and accuracy.
(5) The clearance test cannot be passed unless the analysis of each aerosol sample collected indicates that the airborne concentration does not exceed 0.01 asbestos fibres per cubic centimeter of air.
(6) A competent person must review the results of the visual inspection specified in Section 8(1), and the results of the air sampling specified in Sections 8(3) and 8(4), before determining whether the enclosure can be removed.
(7) If a competent person indicates that the visual inspection or clearance test is not passed, then the clean-up steps specified in Section 7 must be repeated, and the clearance test must be repeated.
(8) If a competent person indicates that the clearance test and visual inspection by a competent person are passed, then the enclosure may be removed.
OCCUPATIONAL HEALTH AND SAFETY ACT
S.N.S. 1996, c. 7
Section 3
3. In this Act,
(a) "aggrieved person" means an employer, constructor, contractor, employee, self-employed person, owner, supplier, provider of an occupational health or safety service, architect, engineer or union at a workplace who is directly affected by an order or decision;
(b) "analyst" means a person appointed as an analyst by the Minister pursuant to this Act;
(c) "Board" means the Labour Board established under the Labour Board Act;
(d) "committee" means a joint occupational health and safety committee established pursuant to this Act;
(e) "compliance notice" means a response, in writing, to an order of an officer, describing the extent to which the person against whom the order was made has complied with each item identified in the order;
(f) "constructor" means a person who contracts for work on a project or who undertakes work on a project himself or herself;
(g) "contractor" means a person who contracts for work to be performed at the premises of the person contracting to have the work performed, but does not include a dependent contractor or a constructor;
(h) "contracts for work" includes contracting to perform work and contracting to have work performed;
(i) "Council" means the Occupational Health and Safety Advisory Council established pursuant to this Act;
(j) "dependent contractor" means a person, whether or not employed under a contract of employment and whether or not furnishing the person's own tools, vehicles, equipment, machinery, material or any other thing, who performs work or services for another on such terms and conditions that the person is
(i) in a position of economic dependence upon the other,
(ii) under an obligation to perform duties mainly for the other, and
(iii) in a relationship with the other more closely resembling that of an employee than an independent contractor;
(k) "Deputy Minister of Labour and Advanced Education" includes a person designated by the Deputy Minister of Labour and Advanced Education to act in the stead of the Deputy Minister;
(l) "Director" means the Executive Director of Occupational Health and Safety or any person designated by the Executive Director pursuant to this Act to act on behalf of the Executive Director;
(m) "Director of Labour Standards" means the Director of Labour Standards under the Labour Standards Code;
(n) "Division" means the Occupational Health and Safety Division of the Department of Labour and Advanced Education;
(o) "employee" means a person who is employed to do work and includes a dependent contractor;
(p) "employer" means a person who employs one or more employees or contracts for the services of one or more employees, and includes a constructor, contractor or subcontractor;
(q) "former Act" means Chapter 320 of the Revised Statutes, 1989, the Occupational Health and Safety Act;
(r) Repealed. [S.N.S. 2010, c. 37, s. 117]
(s) "Minister" means the Minister of Labour and Advanced Education;
(t) "occupation" means any employment, business, calling or pursuit;
(u) "officer" means an occupational health and safety officer appointed pursuant to this Act and includes the Director;
(v) "owner" includes a trustee, receiver, mortgagee in possession, tenant, lessee or occupier of lands or premises used as a workplace and a person who acts for, or on behalf of, an owner as an agent or delegate;
(w) "police officer" means
(i) a member of the Royal Canadian Mounted Police, or
(ii) a member or chief officer of a police force appointed pursuant to the Police Act;
(x) "policy" means an occupational health and safety policy made pursuant to this Act;
(y) "practicable" means possible, given current knowledge, technology and invention;
(z) "program" means an occupational health and safety program required pursuant to this Act, unless the context otherwise requires;
(aa) "project" means a construction project, and includes
(i) the construction, erection, excavation, renovation, repair, alteration or demolition of any structure, building, tunnel or work and the preparatory work of land clearing or earth moving, and
(ii) work of any nature or kind designated by the Director as a project;
(ab) "reasonably practicable" means practicable unless the person on whom a duty is placed can show that there is a gross disproportion between the benefit of the duty and the cost, in time, trouble and money, of the measures to secure the duty;
(ac) "regularly employed" includes seasonal employment with a predictably recurring period of employment that exceeds four weeks, unless otherwise established by regulation or ordered by an officer;
(aca) "repeatedly" means occurring more than once within the preceding three year period;
(ad) "representative" means a health and safety representative selected pursuant to this Act;
(ae) "self-employed person" means a person who is engaged in an occupation on that person's own behalf and includes a person or persons operating a sole proprietorship but does not include a dependent contractor;
(aea) "serious injury" means an injury that endangers life or causes permanent injury;
(af) "supplier" means a person who manufactures, supplies, sells, leases, distributes or installs any tool, equipment, machine or device or any biological, chemical or physical agent to be used at or near a workplace;
(ag) "union" includes a trade union as defined in the Trade Union Act that has the status of bargaining agent under that Act in respect of any bargaining unit at a workplace, and includes an organization representing employees where the organization has exclusive bargaining rights under any other Act in respect of the employees;
(ah) "workplace" means any place where an employee or a self-employed person is or is likely to be engaged in any occupation and includes any vehicle or mobile equipment used or likely to be used by an employee or a self-employed person in an occupation.
[S.N.S. 2000, c. 28, s. 86; 2010, c. 66, s. 2; 2010, c. 37, s. 117; 2011, c. 24, s. 2; 2016, c. 14, s. 1]
Workplace Health and Safety Regulations
N.S. Reg. 52/2013
Part 1 INTERPRETATION AND APPLICATION
Section 1.2 Definitions for these regulations
1.2 In these regulations,
"Act" means the Occupational Health and Safety Act ;
"adequate" means sufficient to protect a person from injury or damage to health;
"ANSI" means the American National Standards Institute;
"anchorage" means a secure connecting point capable of safely withstanding the impact forces, as prescribed in these regulations or an applicable standard, applied by a fall-protection system;
"approved" means approved by the Department or by an agency or authority designated or selected by the Department to make approvals;
"competent person" means a person who is
(i) qualified because of their knowledge, training and experience to do the assigned work in a manner that ensures the health and safety of every person in the workplace, and
(ii) knowledgeable about the provisions of the Act and regulations that apply to the assigned work, and about potential or actual danger to health or safety associated with the assigned work,
"CSA" means the Canadian Standards Association;
"certified" means meeting the requirements of a standard as attested to by a certification organization accredited by the Standards Council of Canada or an engineer;
"Department" means the Department of Labour and Advanced Education;
"designated" means, in relation to an employer, appointed in writing by the employer;
"emergency services agency" means an agency operating within the Province for the purpose of responding to emergencies, including
(i) a municipal police force required to be maintained under the Police Act, including the Royal Canadian Mounted Police,
(ii) fire departments,
(iii) ambulance services;
"engineer" means a person who is registered as a member or licensed to practise under the Engineering Profession Act and is competent to do the work being performed;
"latest version" means, in relation to a standard or other publication, the latest edition of the standard or publication as supplemented, amended, added to, replaced or superseded;
"manufacturer's specifications" means
(i) the written instructions of a manufacturer of a machine, material, tool or equipment that outline the manner in which the machine, material, tool or equipment is to be erected, installed, assembled, started, operated, used, handled, stored, stopped, adjusted, carried, maintained, repaired, inspected, serviced, tested, cleaned or dismantled, and
(ii) a manufacturer's instruction, operating or maintenance manual and drawings respecting a machine, tool or equipment;
"temporary highway workplace" means a temporary workplace on a highway, as defined in Part 24;
"work area" means a location at a workplace where an employee or self-employed person is working or may be required to work.
Occupational Safety General Regulations
N.S. Reg. 44/99
Part 1 Title and Definitions
Section 2 Definitions
2. In these regulations,
(a) "Act" means the Occupational Health and Safety Act ;
(aa) "adequate" means sufficient to protect a person from injury or damage to health;
(b) "ALI" means the Automotive Lift Institute;
(ba) "angle of repose" means the angle with the horizontal at which material will no longer flow freely;
(c) "ANSI" means the American National Standards Institute;
(ca) "approved" means approved by the Department or by an agency or authority designated or selected by the Department to make approvals;
(d) "ASME" means the American Society of Mechanical Engineers;
(e) "ASTM" means the American Society for Testing and Materials;
(ea) "CGA" means the Compressed Gas Association;
(f) "CGSB" means the Canadian General Standards Board;
(g) "competent person" means a person who is
(i) qualified because of their knowledge, training and experience to do the assigned work in a manner that ensures the health and safety of every person in the workplace, and
(ii) knowledgeable about the provisions of the Act and regulations that apply to the assigned work, and about potential or actual danger to health or safety associated with the assigned work;
(ga) "compressed air" means air mechanically raised to a pressure higher than atmospheric pressure;
(h) "CSA" means the Canadian Standards Association;
(i) "demolition" means the destruction or removal of all, or part, of an existing building or structure;
(ia) "Department" means the Department of Labour and Advanced Education;
(j) "designated" means, in relation to an employer, appointed in writing by the employer;
(k) "electrical installation" means the wires, machinery, apparatus, appliances, devices, material and equipment used or intended for use for the generation, transmission, distribution, supply and use of electrical power or energy, and includes a power line and power line equipment;
(l) "engineer" means a person who is registered as a member or licensed to practise under the Engineering Profession Act and is competent to do the work being performed;
(m) "firefighter" means
(i) an employee who provides fire suppression services to the public from a fire department within a municipality or local service district, or
(ii) an industrial firefighter;
(n) "guardrail" means a fall protection system consisting of vertical and horizontal members that
(i) are capable of withstanding concentrated forces, as prescribed in these regulations or an applicable standard,
(ii) warn of a fall hazard, and
(iii) reduce the risk of a fall;
(o) "hazardous substance" means chemical or biological material, dangerous goods within the meaning of the Dangerous Goods Transportation Act or a controlled product within the meaning of the Hazardous Products Act (Canada) that is likely to, because of its harmful nature, cause injury or damage to the health or safety of a person exposed to it;
(p) "hoist" means a device or equipment and its structure used for lifting or lowering material, including cranes, an automotive lift, a winch, a chain fall or other similar device, but does not include a lift truck, a power operated elevating work platform, a device to which the Elevators and Lifts Act applies or a hoist that operates in a shaft in the underground at a mine;
(pa) "ITSDF" means the Industrial Truck Standards Development Foundation;
(q) "industrial firefighter" means an employee who
(i) is designated to fight fires at the employee's place of employment, and
(ii) is employed by an employer who does not, in the normal course of its business, provide fire suppression services to the public;
(qa) "latest version" means, in relation to a standard or other publication, the latest edition of the standard or publication as supplemented, amended, added to, replaced or superseded;
(r) "lift truck" means a lift truck as defined in the latest version of ANSI standard ANSI/ITSDF B56.1, "Safety Standard for Low Lift and High Lift Trucks";
(s) "locked out" means to have
(i) isolated the energy source or sources from a machine, equipment, tool or electrical installation,
(ii) dissipated any residual energy in a system, and
(iii) secured the isolation of the energy source or sources by an inhibiting device that is operated by a key or other process,
and to have performed a "lock-out" has a similar meaning;
(t) "machine" Repealed. [N.S. Reg. 52/2000, s. 1]
(u) "manufacturer's specifications" means
(i) the written instructions of a manufacturer of a machine, material, tool or equipment that outline the manner in which the machine, material, tool or equipment is to be erected, installed, assembled, started, operated, used, handled, stored, stopped, adjusted, carried, maintained, repaired, inspected, serviced, tested, cleaned or dismantled, and
(ii) a manufacturer's instruction, operating or maintenance manual and drawings respecting a machine, tool or equipment;
(ua) "mobile crane" means a mobile crane to which the latest version of CSA standard CSA Z150 , "Safety Code on Mobile Cranes" applies;
(v) "NFPA" means the National Fire Protection Association;
(va) "overhead crane" means any mechanical device or structure that is used to raise, lower and move material that travels overhead and that incorporates a
(i) power driven drum, bridge and cable or rope,
(ii) single or multiple girder, and
(iii) moveable bridge carrying a moveable or fixed hoisting mechanism,
but does not include wall cranes, cantilever gantry cranes and semi-gantry cranes;
(vb) "personal flotation device" means personal protective equipment that is capable of supporting a person with their head above water without the direct effort of the person wearing the equipment;
(w) "power line" means the above-ground or underground wiring that is used to distribute electricity;
(x) "power line equipment" means the components that are required to distribute electricity by means of a power line;
(y) "power operated elevating work platform" means a mobile horizontal working surface that provides access and support to a person at a workplace, and that is elevated and lowered by means of a mechanism and [that complies with] Part 23: Scaffolds and Other Elevated Work Platforms, of the Workplace Health and Safety Regulations made under the Act, including a standard listed in subsection (4) thereof;
(z) "powered mobile equipment" means self-propelled equipment that is designed to operate on land in conditions other than a public highway, but does not include equipment primarily designed to transport persons, a lift truck or a power operated elevating work platform;
(aa) "SAE" means the Society of Automotive Engineers;
(ab) "structural fire-fighting" means the activities of rescue, fire suppression and conservation of property from fires involving buildings, structures, vehicles, vessels, aircraft or other large objects constructed by human effort;
(ac) "surface mine" means a work or undertaking, other than a trench, for the purpose of opening up, proving, removing or extracting any metallic or non-metallic mineral or mineral bearing substance, rock, earth, clay, sand or gravel by means of an open excavation, and includes a pit or quarry;
(ad) "tower crane" means any mechanical device or structure that
(i) incorporates a power-driven drum and cable or rope and a vertical mast or tower and a jib,
(ii) is of the traveling, fixed or climbing type, and
(iii) is used exclusively for raising, lowering and moving material;
(ae)"trench" means an excavation in which the excavation depth exceeds the excavation width;
(af) "work area" means a location at the workplace at which an employee or self-employed person is or is likely to be working;
(ag) "worked" means drilled, blasted, extracted, excavated, loaded or subjected to other similar work.
[N.S. Reg. 52/2000, s. 1; 151/2003; 53/2013, ss. 1, 93]