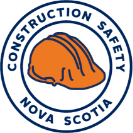
Emergency Eyewash and Showers
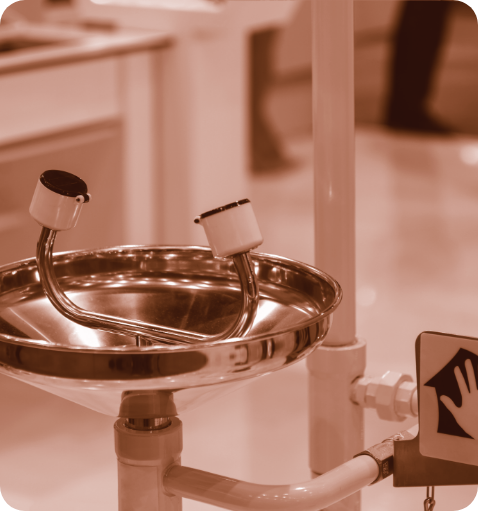
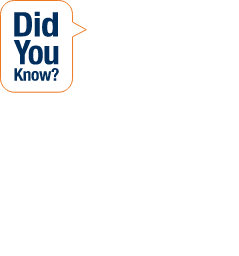
Follow these links
to related legislation
Highlighted words reveal
definitions and supplementary
information when selected
Emergency showers and eyewash stations provide on-the-spot decontamination. They allow workers to flush away hazardous substances that can cause injury. Emergency showers enable the user to have water cascading over the entire body, whereas eyewash stations enable the user to flush the eye and face area only. There are combination units available that contain both features: a shower and an eyewash.
Employers must install emergency eyewash stations or showers when there is a risk that a worker’s eyes or skin may come in contact with hazardous substances in the workplace. Employers are responsible for maintaining and meeting the safety requirements prescribed by the regulations and the manufacturer’s specifications. The design or placement of emergency eyewash and showers must comply with the latest version of ANSI standard ANSI/ISEA Z358.1, "American Standard for Emergency and Shower Equipment."
An employer must:
- Where a person’s skin or eyes may be acutely affected by exposure to a caustic, acidic, or other hazardous substance, provide one of the following in the work area where the exposure may occur:
- an emergency shower;
- an eyewash fountain;
- enough flushing fluid to last at least 15 minutes;
- other equipment sufficient for the removal of the substance.
- Make sure eyewash or shower equipment meets all of the following requirements. It must:
- comply with the requirements of the latest version of ANSI standard ANSI/ISEA Z358.1, "American Standard for Emergency and Shower Equipment";
- be installed, operated, inspected and maintained as per the manufacturer's instructions;
- be located so that there is a clear path to the equipment and the user can access the equipment within 10 seconds of exposure;
- provide sufficient flushing fluid at sufficient pressure for at least 15 minutes, or the time indicated on the Safety Data Sheet(SDS), whichever is greater;
- have the instructions for use and an expiration date permanently affixed to the unit.
- Make sure employees who are required to use the eyewash and shower equipment receive the required information, instruction, and training.
Occupational Safety General Regulations
N.S. Reg. 44/99
Part 1 Title and Definitions
Section 2 Definitions
2. In these regulations,
(a) "Act" means the Occupational Health and Safety Act ;
(aa) "adequate" means sufficient to protect a person from injury or damage to health;
(b) "ALI" means the Automotive Lift Institute;
(ba) "angle of repose" means the angle with the horizontal at which material will no longer flow freely;
(c) "ANSI" means the American National Standards Institute;
(ca) "approved" means approved by the Department or by an agency or authority designated or selected by the Department to make approvals;
(d) "ASME" means the American Society of Mechanical Engineers;
(e) "ASTM" means the American Society for Testing and Materials;
(ea) "CGA" means the Compressed Gas Association;
(f) "CGSB" means the Canadian General Standards Board;
(g) "competent person" means a person who is
(i) qualified because of their knowledge, training and experience to do the assigned work in a manner that ensures the health and safety of every person in the workplace, and
(ii) knowledgeable about the provisions of the Act and regulations that apply to the assigned work, and about potential or actual danger to health or safety associated with the assigned work;
(ga) "compressed air" means air mechanically raised to a pressure higher than atmospheric pressure;
(h) "CSA" means the Canadian Standards Association;
(i) "demolition" means the destruction or removal of all, or part, of an existing building or structure;
(ia) "Department" means the Department of Labour and Advanced Education;
(j) "designated" means, in relation to an employer, appointed in writing by the employer;
(k) "electrical installation" means the wires, machinery, apparatus, appliances, devices, material and equipment used or intended for use for the generation, transmission, distribution, supply and use of electrical power or energy, and includes a power line and power line equipment;
(l) "engineer" means a person who is registered as a member or licensed to practise under the Engineering Profession Act and is competent to do the work being performed;
(m) "firefighter" means
(i) an employee who provides fire suppression services to the public from a fire department within a municipality or local service district, or
(ii) an industrial firefighter;
(n) "guardrail" means a fall protection system consisting of vertical and horizontal members that
(i) are capable of withstanding concentrated forces, as prescribed in these regulations or an applicable standard,
(ii) warn of a fall hazard, and
(iii) reduce the risk of a fall;
(o) "hazardous substance" means chemical or biological material, dangerous goods within the meaning of the Dangerous Goods Transportation Act or a controlled product within the meaning of the Hazardous Products Act (Canada) that is likely to, because of its harmful nature, cause injury or damage to the health or safety of a person exposed to it;
(p) "hoist" means a device or equipment and its structure used for lifting or lowering material, including cranes, an automotive lift, a winch, a chain fall or other similar device, but does not include a lift truck, a power operated elevating work platform, a device to which the Elevators and Lifts Act applies or a hoist that operates in a shaft in the underground at a mine;
(pa) "ITSDF" means the Industrial Truck Standards Development Foundation;
(q) "industrial firefighter" means an employee who
(i) is designated to fight fires at the employee's place of employment, and
(ii) is employed by an employer who does not, in the normal course of its business, provide fire suppression services to the public;
(qa) "latest version" means, in relation to a standard or other publication, the latest edition of the standard or publication as supplemented, amended, added to, replaced or superseded;
(r) "lift truck" means a lift truck as defined in the latest version of ANSI standard ANSI/ITSDF B56.1, "Safety Standard for Low Lift and High Lift Trucks";
(s) "locked out" means to have
(i) isolated the energy source or sources from a machine, equipment, tool or electrical installation,
(ii) dissipated any residual energy in a system, and
(iii) secured the isolation of the energy source or sources by an inhibiting device that is operated by a key or other process,
and to have performed a "lock-out" has a similar meaning;
(t) "machine" Repealed. [N.S. Reg. 52/2000, s. 1]
(u) "manufacturer's specifications" means
(i) the written instructions of a manufacturer of a machine, material, tool or equipment that outline the manner in which the machine, material, tool or equipment is to be erected, installed, assembled, started, operated, used, handled, stored, stopped, adjusted, carried, maintained, repaired, inspected, serviced, tested, cleaned or dismantled, and
(ii) a manufacturer's instruction, operating or maintenance manual and drawings respecting a machine, tool or equipment;
(ua) "mobile crane" means a mobile crane to which the latest version of CSA standard CSA Z150 , "Safety Code on Mobile Cranes" applies;
(v) "NFPA" means the National Fire Protection Association;
(va) "overhead crane" means any mechanical device or structure that is used to raise, lower and move material that travels overhead and that incorporates a
(i) power driven drum, bridge and cable or rope,
(ii) single or multiple girder, and
(iii) moveable bridge carrying a moveable or fixed hoisting mechanism,
but does not include wall cranes, cantilever gantry cranes and semi-gantry cranes;
(vb) "personal flotation device" means personal protective equipment that is capable of supporting a person with their head above water without the direct effort of the person wearing the equipment;
(w) "power line" means the above-ground or underground wiring that is used to distribute electricity;
(x) "power line equipment" means the components that are required to distribute electricity by means of a power line;
(y) "power operated elevating work platform" means a mobile horizontal working surface that provides access and support to a person at a workplace, and that is elevated and lowered by means of a mechanism and [that complies with] Part 23: Scaffolds and Other Elevated Work Platforms, of the Workplace Health and Safety Regulations made under the Act, including a standard listed in subsection (4) thereof;
(z) "powered mobile equipment" means self-propelled equipment that is designed to operate on land in conditions other than a public highway, but does not include equipment primarily designed to transport persons, a lift truck or a power operated elevating work platform;
(aa) "SAE" means the Society of Automotive Engineers;
(ab) "structural fire-fighting" means the activities of rescue, fire suppression and conservation of property from fires involving buildings, structures, vehicles, vessels, aircraft or other large objects constructed by human effort;
(ac) "surface mine" means a work or undertaking, other than a trench, for the purpose of opening up, proving, removing or extracting any metallic or non-metallic mineral or mineral bearing substance, rock, earth, clay, sand or gravel by means of an open excavation, and includes a pit or quarry;
(ad) "tower crane" means any mechanical device or structure that
(i) incorporates a power-driven drum and cable or rope and a vertical mast or tower and a jib,
(ii) is of the traveling, fixed or climbing type, and
(iii) is used exclusively for raising, lowering and moving material;
(ae)"trench" means an excavation in which the excavation depth exceeds the excavation width;
(af) "work area" means a location at the workplace at which an employee or self-employed person is or is likely to be working;
(ag) "worked" means drilled, blasted, extracted, excavated, loaded or subjected to other similar work.
[N.S. Reg. 52/2000, s. 1; 151/2003; 53/2013, ss. 1, 93]
Part 4 Ventilation, Lighting, Sanitation and Accommodation
Section 23 Emergency showers and eyewashes
23. (1) Where a person's skin or eyes may be acutely affected by an exposure to a caustic, acidic or other hazardous substance, an employer shall provide 1 of the following in the work area where the exposure may occur:
(a) an emergency shower;
(b) an eye wash fountain;
(ba) enough flushing fluid to last at least 15 minutes;
(c) other equipment sufficient for removal of the substance.
(2) An eye wash or shower equipment that is used must meet all of the following requirements:
(a) it must comply with the requirements of the latest version of ANSI standard ANSI/ISEA Z358.1, "American Standard for Emergency and Shower Equipment";
(b) it must be installed, operated, inspected and maintained in accordance with the manufacturer's instructions;
(c) it must be located so that there is an unobstructed path to the equipment and the user can access the equipment within 10 seconds of exposure;
(d) it must provide sufficient flushing fluid at sufficient pressure for the greater of
(i) 15 minutes, and
(ii) the time indicated on the MSDS sheet;
(e) it must have the instructions for use and an expiration date permanently affixed to the unit.
[N.S. 53/2013, s. 16]
OCCUPATIONAL HEALTH AND SAFETY ACT
S.N.S. 1996, c. 7
Section 13 DUTIES AND PRECAUTIONS
13. (1) Every employer shall take every precaution that is reasonable in the circumstances to
(a) ensure the health and safety of persons at or near the workplace;
(b) provide and maintain equipment, machines, materials or things that are properly equipped with safety devices;
(c) provide such information, instruction, training, supervision and facilities as are necessary to the health or safety of the employees;
(d) ensure that the employees, and particularly the supervisors and foremen, are made familiar with any health or safety hazards that may be met by them at the workplace;
(e) ensure that the employees are made familiar with the proper use of all devices, equipment and clothing required for their protection; and
(f) conduct the employer's undertaking so that employees are not exposed to health or safety hazards as a result of the undertaking.
(2) Every employer shall
(a) consult and co-operate with the joint occupational health and safety committee, where such a committee has been established at the workplace, or the health and safety representative, where one has been selected at the workplace;
(b) co-operate with any person performing a duty imposed or exercising a power conferred by this Act or the regulations;
(c) provide such additional training of committee members or the representative as may be prescribed by the regulations;
(d) comply with this Act and the regulations and ensure that employees at the workplace comply with this Act and the regulations; and
(e) where an occupational health and safety policy or occupational health and safety program is required pursuant to this Act or the regulations, establish the policy or program.
(3) The employer at a subsea coal mine shall provide such additional resources or information for the committee as may be prescribed by the regulations.
[N.S. 2007, c. 14, s. 7; 2010, c. 66, s. 5]
Workplace Health and Safety Regulations
N.S. Reg. 52/2013
Part 21 FALL PROTECTION
Section 21.4 Written fall-protection safe-work plan
21.4 (1) Except as provided in subsection (2), an employer must establish a specific written fall-protection safe-work plan for a specific work area where fall protection is required and the fall distance is 7.5 m or more.
(2) A specific written fall-protection safe-work plan is not required under subsection (1) if any of the following conditions apply:
(a) all persons performing the work are protected by a permanent guardrail;
(b) the work is performed from a work-platform described in Sections 23.12 to 23.15 of Part 23: Scaffolds and Other Elevated Work-platforms and all persons performing the work are using adequate fall protection;
(c) the work is performed by an emergency services agency in accordance with Section 1.16.
(3) A fall-protection safe-work plan must be established based on a hazard assessment of the specific work to be performed in the work area and must include all of the following information:
(a) the nature of the work to be performed;
(b) the anticipated duration of the work;
(c) a description of the work;
(d) a list of the primary tools or equipment to be used in the work;
(e) reference to applicable health and safety legislation and regulations;
(f) a list of potential fall hazards of the work and their associated risks;
(g) the fall-protection system or systems to be used at the work area;
(h) any anchorages to be used during the work;
(i) if a fall-arrest system is to be used, confirmation that the clearance distances below the work area are sufficient to prevent a person from striking
(i) the nearest safe surface or water,
(ii) a surface or thing that could cause injury to the person on contact, or
(iii) exposed hazardous material, such as an open tank, pit or vat;
(j) a procedure to address the risks associated with the potential for swing as a result of anchorage placement when a person is using a fall-arrest system;
(k) the procedures to be used to assemble, maintain, inspect, use and disassemble a fall-protection system, as applicable;
(l) schedules for inspecting any fall-protection systems and the names of any persons responsible for carrying out the inspections;
(m) adequate written rescue procedures to be used if a person falls and requires rescue, including if a person is suspended by a fall-arrest system or personnel safety net;
(n) the effect of weather conditions;
(o) the name of a designated competent person to supervise the work area;
(p) the training and qualifications required for persons who will perform the work, as determined by the employer;
(q) a method for communicating the fall-protection safe-work plan to any person who may be affected by the plan.
(4) If a workplace has more than 1 work area for which a fall-protection safe-work plan is required, an employer may create a separate plan for each specific work area or one overall plan for the workplace that includes all of the requirements necessary for each specific plan.